High-Performance CNC Spindle Selection Guide: Choose the Right Lathe Spindle to Boost Machining Efficiency
Unveiling the Core Player in CNC Machining
For most people, the term “lathe spindle” might sound unfamiliar. Just remember this: the spindle is the core component that connects the cutting tool to the machine in CNC machining, and it directly affects machining accuracy, efficiency, and service life. In this article, we’ll take you from zero to hero—quickly covering the spindle’s functions, types, and selection logic—and show how FEPO Industrial applies precision technology to create more stable and durable spindle solutions.
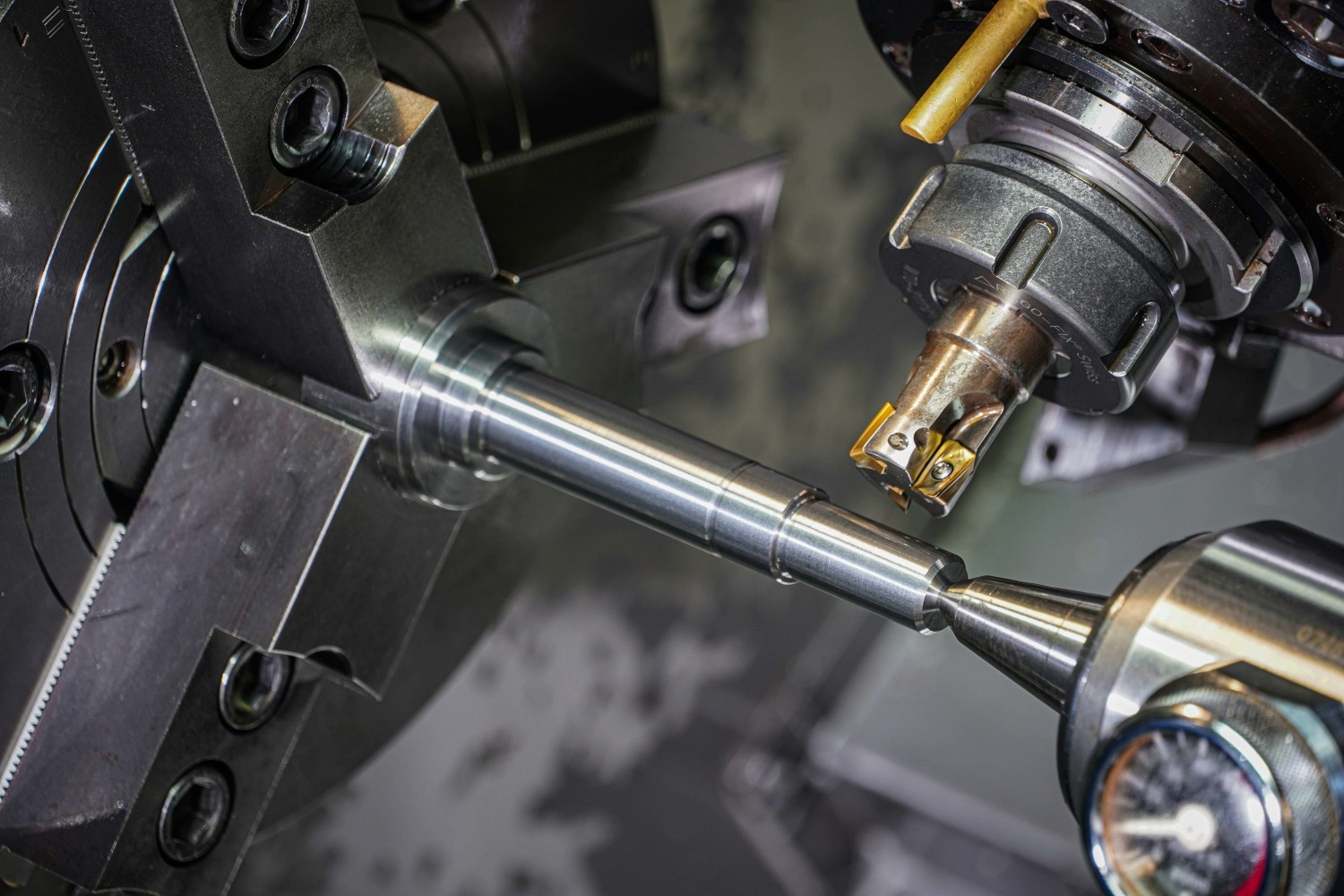
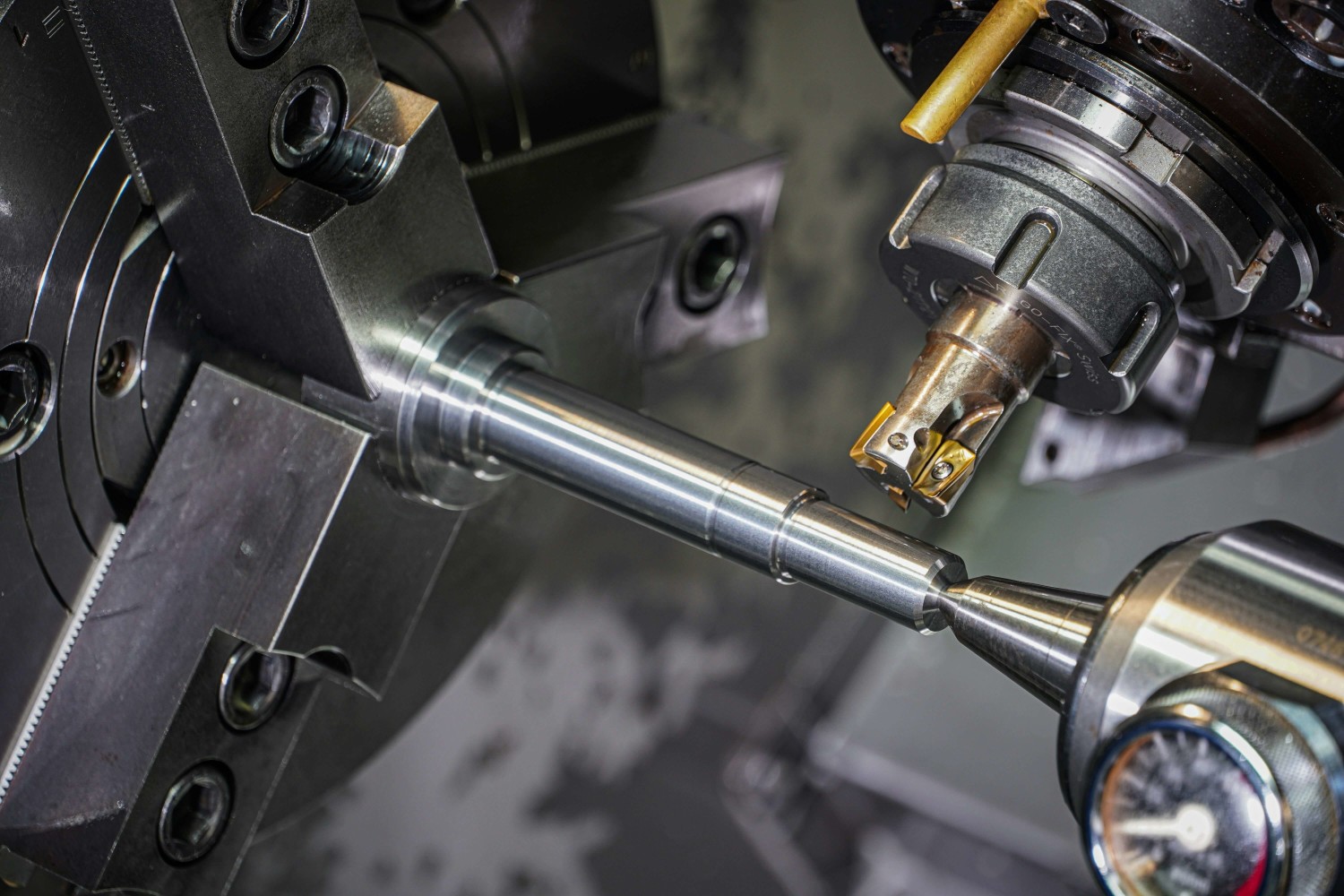
Basic Structure and Working Principle of the Spindle
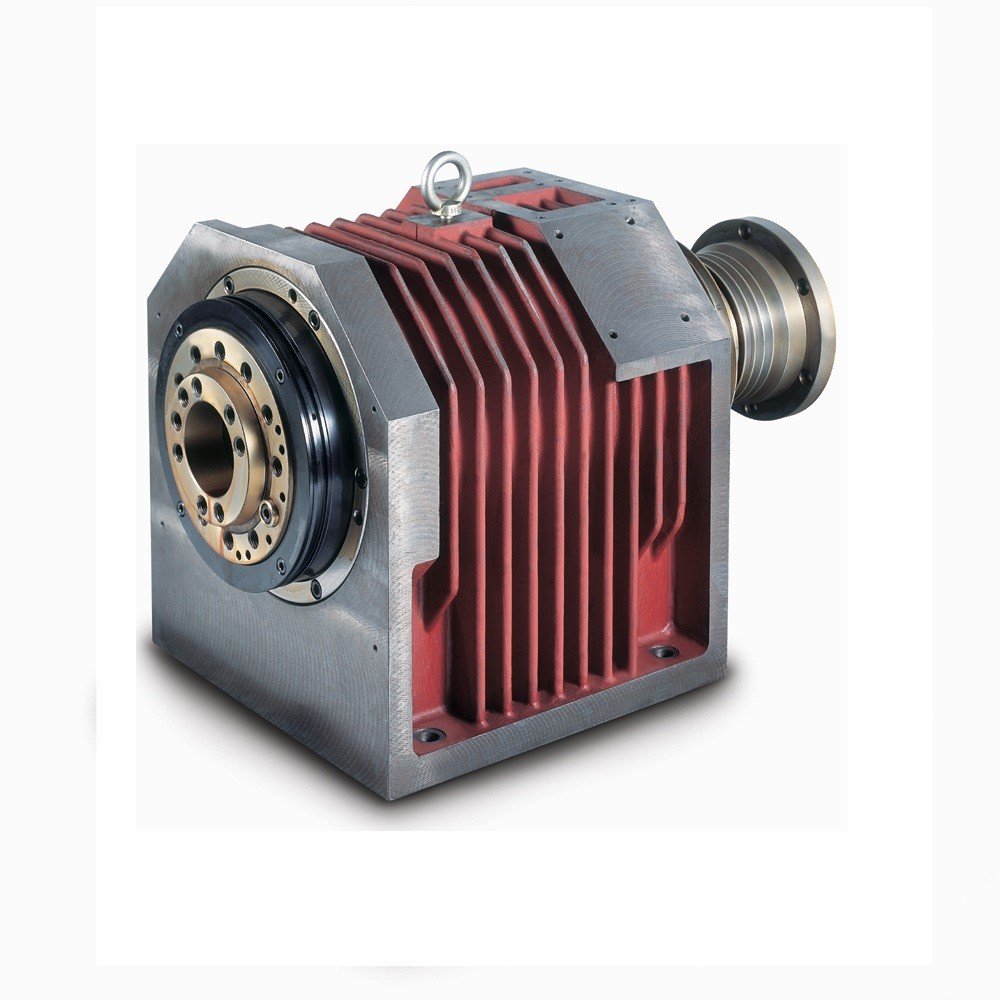
Analysis of Mainstream Spindle Types
Common spindle designs on the market fall into four major categories: built‑in spindle, direct‑drive spindle, belt‑drive spindle, and electro‑spindle. Each design suits different machining scenarios and offers its own structural advantages. Choosing the right type can significantly boost CNC machining performance.
Built‑in Spindle
This design integrates the motor and spindle body into one unit, eliminating transmission elements. Its compact structure and excellent rigidity, plus uniform heat distribution and low vibration, maintain stable accuracy during machining. You’ll often find them in 5‑axis machining centers and small, high‑precision lathes—ideal for applications demanding both precision and efficient space utilization.
Direct‑Drive Spindle
Here, the motor is mounted directly on the spindle end, removing belt or gear drive losses. With very high power‑transmission efficiency and rapid response to cutting demands, this type is key in today’s high‑speed machining trend. Its simple construction minimizes energy loss, though it places stricter precision requirements on the motor and bearings themselves.
Belt‑Drive Spindle
Compared with the more modern options above, the belt‑drive spindle is a traditional and economical choice. Power is transmitted via belts and pulleys; while it lags slightly in efficiency and speed stability, its simple structure and easy maintenance make it popular in many mid‑ to low‑speed machines. For users on a tight budget or retrofitting existing equipment, it offers excellent value.
Electro‑Spindle
An electro‑spindle is a highly integrated unit combining the motor, spindle, cooling, and control systems into a single module. This design not only saves space but also allows plug‑and‑play operation—ideal for highly automated production lines or mold‑making operations. Although the initial investment is higher, it reduces long‑term downtime and maintenance, excelling in both efficiency and stability.
Each spindle design answers different “machining requirements.” When choosing, consider not only precision and speed but also budget, machine‑room space, and maintenance capabilities to find the optimal combination.
FEPO Spindle Features and Advantages
FEPO commitment to quality shows in every spindle assembly and inspection process. All spindles are assembled in a strictly temperature‑ and humidity‑controlled environment to ensure geometric tolerances between parts remain within 2 μm, then dynamically balanced to the optimal state. Long‑duration thermal stability tests verify that the thermal‑deformation curve stays flat during continuous machining, preventing thermal expansion and contraction from affecting accuracy. Critical double‑row cylindrical roller bearings use the high‑performance NN30 series, analyzed with blue contact‑area agents to ensure even load distribution and smoother rotation. FEPO’s proprietary LAPPING machining techniques and high‑precision grinding‑wheel dressing systems control the roundness of the spindle tailstock and accessories to within 2 μm, keeping noise low and service life long even under heavy loads.
How to Choose the Right CNC Spindle
High‑speed precision grinding: recommend built‑in spindle + LAPPING‑machined tailstock.
Large‑volume rough cutting: direct‑drive or electro‑spindle with high‑rigidity bearings.
Budget and Maintenance Costs
Belt‑drive spindle has the lowest initial investment but requires frequent belt replacements and tension adjustments.
Electro‑spindle is more expensive upfront but eliminates extra components, making maintenance simpler.
Environment and Machine‑Room SpaceSmall workshops or high mobility needs: give priority to electro‑spindle or built‑in spindle.
Retrofitting traditional equipment: belt‑drive or direct‑drive spindles offer greater flexibility.
Stability TestingRequest dynamic‑balance reports and thermal‑rise test results to confirm tolerances and temperature curves.
FEPO’s constant‑temperature, constant‑humidity assembly and multi‑stage quality inspections let you proceed with confidence.
Years of hands‑on experience and accumulated know‑how enable FEPO to recommend the most suitable spindle systems and solutions for customers with diverse needs.